- High pressure – High mechanical strength
- Complex shape – High formability
- Corrosive media – High corrosion resistance
- Efficient heat transfer – High thermal conductivity
What are the possibilities for using duplex stainless steels?
The most commonly used materials for PHE applications are the highly ductile and corrosion-resistant austenitic stainless steel alloys such as 304L, 316L, and higher alloyed versions such as super-austenitic 6% Mo grades for harsher environments. Other materials such as nickel and titanium alloys are also alternatives for use with extremely corrosive media, as well as copper alloys which provide very good heat transfer properties.If the starting point in designing a PHE is to select stainless steel for its corrosion resistance, then it makes sense to consider duplex grades for their higher strength. The acceptable design stresses for different duplex alloys are up to two times higher than those provided by austenitic grades with no nitrogen addition – according to the applicable design standards (e.g., ASME VIII, EN 13445).
If the strength advantage of duplex can be utilized, then it is possible to use thinner gauges or higher working pressures. The use of thinner plates will also improve the heat transfer capacity. Duplex alloys also offer a somewhat higher heat conductivity.
To evaluate the potential for using a duplex alloy in a PHE, the key parameter is its forming properties. Duplex stainless steels have a lower formability than most austenitic grades, with a fracture elongation of about 25% versus 40%. More ductile duplex alloys, such as Forta FDX 27 (1.4637, S82031), utilize the Transformation Induced Plasticity (TRIP) effect to further improve their formability to a level approaching austenitic alloys. However, its corrosion resistance is not always suitable for harsh conditions.
Therefore, when designing a PHE for harsher environments, we need to ask if conventional Forta DX 2205, or even super-duplex Forta SDX 2507, offers a suitable alternative to the more expensive high-alloy austenitic grades? The critical material properties of duplex and austenitic grades are illustrated in Figures 1 and 2.
![]() |
![]() |
Fig.1 Comparision of mechanical strength vs corrosion resistance | Fig.2 Comparision of mechanical strength vs. ductility |
Using a Forming Limit Diagram (FLD)
Rather than looking only at elongation, a forming limit diagram (FLD) is a better tool to assess the formability of complex metal sheet. This diagram illustrates the three main forming conditions of plane strain, stretch forming, and deep drawing, as shown in Figure 3.
Fig. 3 - FLD at different forming conditions
For PHE sheets there are different types of strain conditions depending on the specific shape of the pattern and the radii and height of the corrugations, which influence the flow and heat transfer capacity. The complexity of the shape has a strong impact on the tool design and how the forming operation can be performed using a certain material.
Figure 4 below shows the typical forming limit curves (FLCs) for three different types of stainless steels.
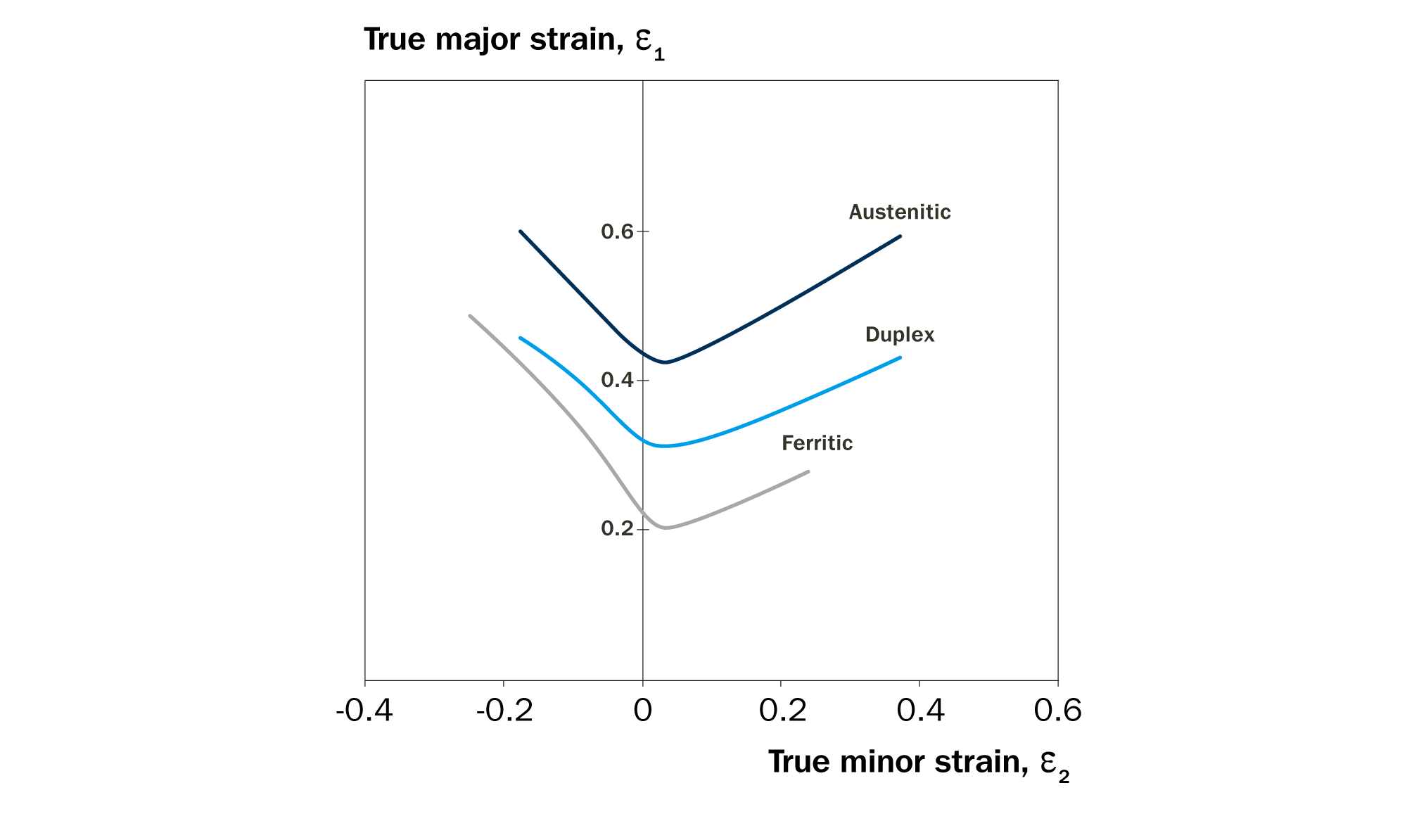
The austenitic grade provides the best formability under all strain conditions, and the ferritic grade the worst. Although, in relative terms, the ferritic grade performs better in deep drawing. The duplex type, with its dual microstructure, sits in-between.
The complex shape of a PHE plate is really challenging for material performance. The formability would be typically highest when biaxially strained, and lowest in the plane strain condition. Therefore, complex plates often fail under this condition. The sheet thickness also influences the formability – a thinner gauge depresses the FLC. This brings further challenges when using a duplex grade, considering that its higher strength enables a reduction in plate thickness.
To evaluate the feasibility of using a duplex material, one approach is to carry out a forming trial with the existing tooling for the austenitic grade. A grid pattern is then applied to the
blank that makes it possible to use a camera to record and measure the strains after forming, so that they can be compared with the FLC for the same alloy and thickness.
Trial project with Forta DX 2205
The grid pattern analysis was used as part of a trial by the Chinese heat exchanger manufacturer Gansu Lanke Petrochemical Equipment Co., Ltd. (LANPEC), under the leadership of Prof. Chunmei Chang.
The goal of the intensive technical collaboration between Outokumpu and LANPEC was to replace 316L with 0.6 mm Forta DX 2205 sheet for a welded PHE. This was to be deployed in an overhead condenser as part of an atmospheric distillation column in an oil refinery. Previously, the plate design had been considered impossible to produce – a sample is shown in Figure 5.
Fig. 5 – A sample of the heat exchanger plate displaying the complex pressed pattern.
Figure 6 shows the strain measurements, indicating that the area most prone to cracking is in the bottom radius of the protrusion in the rolling direction of the sheet, where plane strain conditions prevail. The margin of failure is about 5% strain. However, the most strained area is located at the end point of the ridge where thinning has occurred due to stretch forming conditions. Yet, the margin of failure is about 15% strain. A common guideline is to include a safety margin of about 10 to 15% strain below the FLC to avoid failure.
The test showed that it was possible to use the existing tooling for Forta DX 2205 without causing any failure. Nevertheless, to ensure a robust and predictable solution, minor changes in the pattern were recommended. These were smoothing out the critical radii to reduce both the critical plain strain conditions and to reduce the degree of thinning.
In practice, the all-welded PHE, using Forta DX 2205, was shown to provide a considerably longer service life than 316L. This lowered OPEX for the plant through reduced shutdown, repair and replacement costs. It has been followed by numerous other successful trials such the SINOPEC installation shown in Figure 7.
![]() |
![]() |
Fig. 6 - FLC compared with strain measurements of the heat exchanger plate.
Duplex for sour applications
Recently, refining and petrochemical plants have encountered even more corrosive sour crude products which reached the limit of Forta DX 2205 for some PHE applications. Therefore, we continued to work on the development of the more resistant, but less ductile, super-duplex grade Forta SDX 2507 as an alternative to more expensive super-austenitic and titanium alloys.
This work has resulted in the consistent production of welded PHEs using Forta SDX 2507. Now, both Forta DX 2205 and Forta SDX 2507 are used widely for PHE applications in oil refining, chemical and pharmaceutical industries, for environmental protection, in nonferrous metal industries and wastewater treatment.
The case is proven for duplex stainless steels in PHE applications
- Higher design stresses can be tolerated than for austenitic grades – allowing for higher working pressure or thinner plates.
- Relatively complex flow patterns can be pressed using similar forming tools to austenitic materials, with the support of Outokumpu’s expertise.
- Cost-effective solutions can be realized with the superior properties of duplex grades to improve heat exchanger performance. Higher corrosion resistance delivers reliable operation and a potentially longer service life for optimized life cycle cost (LCC).